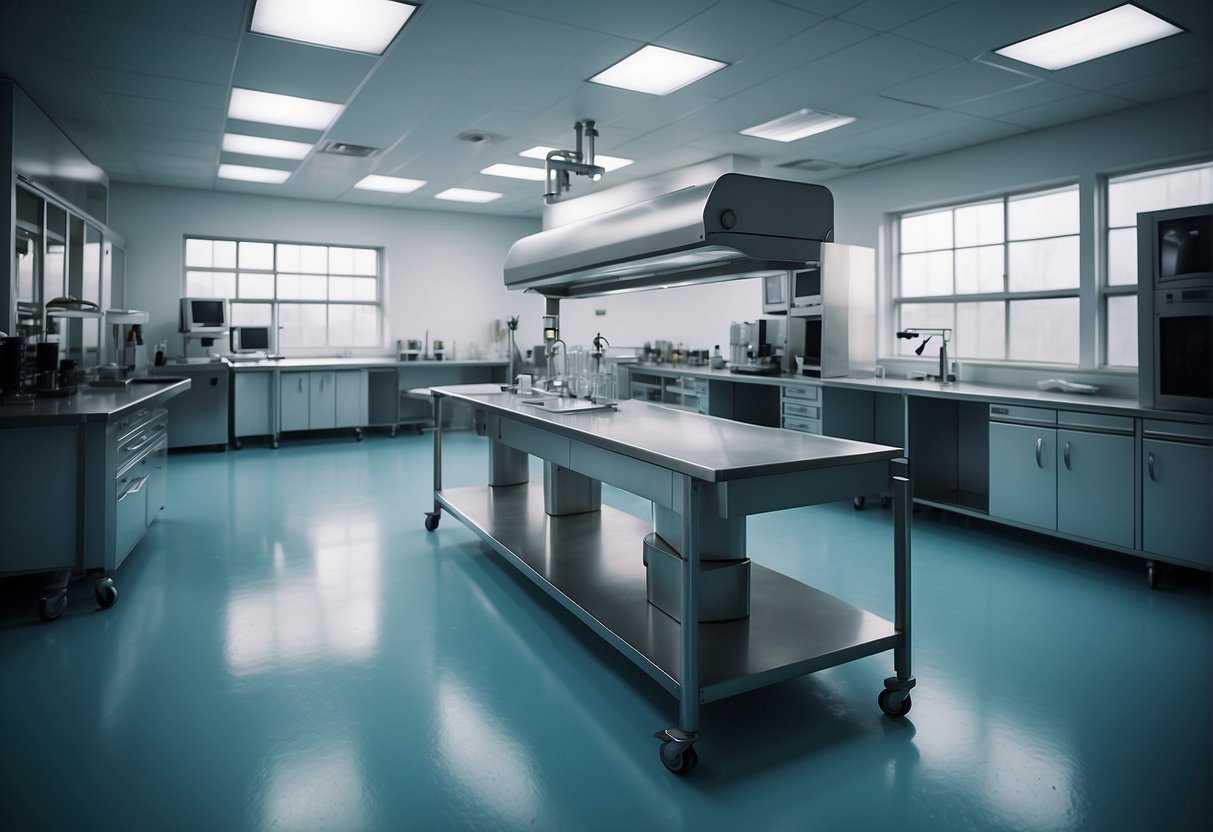
In the highly regulated field of medical device manufacturing, maintaining a controlled environment is paramount for both compliance and quality assurance. Cleanrooms are fundamental in ensuring that products meet the required standards, free from contaminants that could compromise their safety and effectiveness. Conventional cleanrooms are typically stationary facilities, but with the advent of modular and portable cleanrooms, you now have the flexibility to set up such controlled environments almost anywhere.
Understanding Cleanrooms in Medical Device Manufacturing
In the realm of medical device manufacturing, your production processes must adhere to stringent standards to ensure product safety and efficacy. Cleanrooms are vital in achieving the required cleanliness and sterility.
According to the World Health Organization (WHO), in high-income countries, about 7 in 100 patients, and in low- and middle-income countries, about 15 in 100 patients acquire healthcare-associated infections (HAI) during hospitalization. Tragically, one in every ten affected patients will succumb to these infections. One key aspect of reducing infections is ensuring that medical devices and supplies are manufactured in sterile conditions.
Definition and Importance of a Cleanroom
A cleanroom is a controlled environment where pollutants like dust, airborne microbes, and aerosol particles are filtered out to provide the cleanest area possible. For medical device cleanrooms, maintaining a sterile environment is crucial to prevent contamination that could compromise patient safety. Following Good Manufacturing Practice (GMP) and standards such as ISO 13485, which is specific to medical devices, cleanrooms ensure your products meet the necessary health regulations.
Cleanroom Classifications and Standards
The standard that details cleanroom specifications and classifications is ISO 14644. This outlines the air cleanliness classes and the corresponding number of allowable particles in the air per cubic meter. For instance, an ISO 7 cleanroom is one of the most common classifications in medical device manufacturing, permitting no more than 352,000 particles sized 0.5µm or larger per cubic meter.
The table below lists different ISO class numbers and the permitted particle counts:
ISO Class | Particles ≥0.1 µm/m³ | Particles ≥0.2 µm/m³ | Particles ≥0.5 µm/m³ | Particles ≥5 µm/m³ |
---|---|---|---|---|
ISO 1 | 10 | 2 | – | – |
ISO 2 | 100 | 24 | – | – |
… | … | … | … | … |
ISO 7 | – | – | 352,000 | 2,930 |
ISO 8 | – | – | 3,520,000 | 29,300 |
Modular and Portable Cleanroom Solutions
When you're looking to meet stringent cleanroom standards in the medical device manufacturing industry, portable and modular cleanroom solutions offer a quick and efficient way to establish a controlled environment. These systems are designed for flexibility and are conducive to fast-paced industrial needs.
A portable cleanroom offers the added advantage of flexibility and adaptability. According to the American Cleanroom Systems, portable cleanrooms are self-contained units that can be relocated without disassembly. These cleanrooms can be constructed on a 40×8 trailer, allowing them to be easily transported to various locations.
Portable cleanrooms provide a versatile option for your manufacturing processes, enabling you to quickly establish a sterile space. These mobile units can come equipped with HEPA filters, softwall curtains, and strip doors, effectively mimicking the stringent environmental controls found in permanent cleanrooms. Whether you need to scale up production temporarily or require a cleanroom at a remote location, portable cleanrooms are an inexpensive and efficient solution.
The modular design of these cleanrooms allows for rapid construction and flexibility in layout, catering to the bespoke needs of your medical device production. These modular units can be equipped with air conditioners, sealed lighting, and other essentials such as pass-thru chambers to minimize the risk of contamination. When consistency and contamination prevention are your top priorities, the choice of portable and modular cleanrooms can support your medical device manufacturing needs without the constraint of a fixed location.
Benefits of Modular Design
Modular cleanrooms are engineered with interchangeable parts that allow for easy expansion or reconfiguration, adapting to your project's scale and requirements. Unlike traditional construction, these modular systems typically require less time to construct and are more cost-effective. They maintain rigorous standards for particle contamination and are available up to ISO 5 classification, ensuring a controlled environment that adheres to your specific industry regulations.
Portable Cleanroom Applications
Your manufacturing process can benefit from portable cleanrooms, especially when there is a need for temporary or movable clean spaces. They are invaluable for short-term projects or when bringing a controlled environment directly to a critical site is necessary. These flexible solutions are also used during facility maintenance or when additional clean space is required quickly to meet increased production demands.
Customization and Scalability of Cleanrooms
Custom cleanroom designs can cater to the specific needs of medical device manufacturing, offering tailored modular cleanroom systems. Scalability ensures that as your production requirements grow, your cleanroom can grow with you. These custom cleanroom options can include integrated HEPA filtration, humidity control, temperature regulation, and specific material compatibility, allowing for a truly controlled environment that meets your exact specifications.
Key Components of Portable Cleanrooms
When you're setting up a cleanroom, especially for medical device manufacturing, every component must adhere to stringent standards to ensure a contaminant-free environment.
HEPA Filtration and Air Handling
High-Efficiency Particulate Air (HEPA) filtration is the cornerstone of cleanroom air purity. The air you breathe in these spaces passes through HEPA filters capable of trapping particles as small as 0.3 microns with an efficiency of 99.97%. In conjunction with air handling systems, these filters maintain a constant flow of purified air, which is crucial for meeting regulatory cleanroom standards, such as ISO 5, ISO 6, and ISO 7.
Material and Construction
The materials and construction of a cleanroom are pivotal to its function. Modular walls facilitate easy assembly and customization, corresponding to the unique needs of your cleanroom, whether you need a hardwall or softwall cleanroom. Surfaces are made from non-particulate shedding materials, often stainless steel or coated aluminum, to further inhibit contamination.
Cleanroom Doors and Pass-Thru Chambers
To maintain a contamination-controlled environment, cleanroom doors are designed for minimal air disturbance upon entry and exit. They are typically constructed with interlocking mechanisms to prevent both doors from being open simultaneously, which would otherwise compromise the cleanroom's integrity. Pass-thru chambers serve a similar purpose, allowing for the transfer of materials into and out of the cleanroom without contaminating the controlled environment. These chambers are essential for process flow efficiency and maintaining cleanliness. Medical device manufacturing relies on such mechanisms to uphold the stringent cleanliness requirements.
Regulatory Compliance and Quality Control
In the medical device industry, complying with regulatory requirements is as vital as the quality of the products themselves. Your attention to these standards ensures patient safety and maintains the integrity of your operations.
Understanding FDA Regulations
Regulatory requirements set by the FDA are the cornerstone of medical device manufacturing in the United States. Good Manufacturing Practices (GMP) and FDA regulations ensure your cleanroom and manufacturing processes meet specific quality benchmarks. The FDA mandates cleanroom operations to control environmental parameters like particulate levels and microbiological contaminants, as stipulated in 21 CFR Part 820.
Global Standards for Quality Control
Internationally, the medical device industry often refers to ISO 13485 as the standard for quality management systems. You need to comply with this standard if you're involved in any part of the lifecycle of a medical device. ISO 13485 focuses on risk management and consistent design, development, and production processes.
Quality Assurance in Cleanroom Operations
Your cleanroom's design and ongoing operations play a pivotal role in quality assurance. This involves monitoring critical parameters such as temperature, humidity, and particulate count. Regularly performed internal audits and validation activities ensure the cleanroom is functioning within the required cleanroom classification – for example, ISO 7 and ISO 8 standards specify the air cleanliness in terms of the number of particles and the required air changes per hour.
Implementation of Portable Cleanroom Technology
In medical device manufacturing, the implementation of cleanroom technology ensures the quality and integrity of products. Through advancements such as AI and automated systems, modular installation techniques, and diligent maintenance, you can leverage innovative solutions for optimal cleanroom operation.
AI and Automation in Cleanrooms
The introduction of AI (Artificial Intelligence) has revolutionized the operation of cleanrooms, providing you with cutting-edge solutions for contamination control. By integrating AI, your cleanroom's environmental monitoring becomes highly efficient, drastically reducing human error. Automated systems can continuously analyze particle counts and environmental conditions, alerting you to any deviations in real time. This level of oversight secures the quality of your medical devices throughout the manufacturing process.
Cleanroom Installation and Validation
Your adoption of modular cleanroom installation offers a flexible and scalable approach to cleanroom construction. These pre-fabricated units can be quickly assembled on site, which significantly cuts down on installation time without compromising structural integrity or performance. Post-installation, strict validation procedures are crucial. You should ensure that your cleanroom meets industry standards such as ISO 14644, confirming that classification and cleanliness levels are within the required limits for your specific manufacturing needs.
Validation Steps:
- Installation Qualification (IQ)
- Operational Qualification (OQ)
- Performance Qualification (PQ)
Maintenance and Upkeep
Regular maintenance is the backbone of a cleanroom's performance. To maintain a contamination-free environment, you must adhere to a rigorous cleaning protocol and schedule equipment servicing. Effective cleanroom solutions typically include HEPA filter replacements, surface cleaning, and monitoring of gowning procedures. By keeping a stringent check on the upkeep, you're ensuring the cleanroom remains compliant with necessary standards and thereby preserving the integrity of the medical devices produced within.
Industry Applications of Cleanrooms
In the world of manufacturing, certain products require environments that eliminate the possibility of contamination. You’ll find cleanrooms at the heart of production areas where the utmost precision is paramount, such as in medical device manufacturing and pharmaceuticals.
Medical and Pharmaceutical
Medical Device Manufacturing: You rely on medical devices to be safe and sterile upon use. That's why medical device manufacturers maintain portable cleanrooms that adhere to stringent standards, largely dictated by ISO classifications. In these controlled environments, every minute detail is managed – from the particulate count in the air to the workflow and packaging. This ensures that medical equipment, spanning from simple bandages to complex diagnostic machines, is produced without the risk of microbial, dust, or aerosol contamination.
-
Packaging: Once the device components are assembled and tested, the packaging stage demands a similar level of cleanliness. In your cleanroom, packaging materials also undergo sterilization processes to ensure a safe barrier that guards against any potential contamination up to the point of use in medical settings.
-
Medical Device Assembly: In the assembly phase, cleanrooms are vital for the systematic piecing together of complex components. Here, the environment is frequently monitored and controlled for factors such as temperature, humidity, and filtration to guarantee that the final products meet all required standards for medical use.
-
Pharmaceuticals: When it comes to the production and handling of pharmaceuticals, sterile environments are not just a preference, they are mandatory. Cleanrooms allow you to maintain the purity of drugs, from synthesis to packaging, assisted by advanced air filtration systems that remove impurities, which can otherwise alter the effects of your pharmaceutical products.
In the context of broader industry applications outside of medical and pharmaceutical sectors, cleanrooms play an essential role in areas like aerospace, defense, and e-liquid manufacturing, each requiring tailored cleanroom specifications to meet their particular industry standards. But in the realm of medical applications, the precision and sanitation provided by cleanrooms are not just about product perfection – they're about preserving life and health.
Safe Practices and Personnel Training
Adherence to strict cleanroom protocols is mandatory for ensuring sterility and patient safety. Proper training for portable cleanroom operators plays a crucial role in maintaining these standards and preventing cross-contamination.
Ensuring Sterility and Patient Safety
Sterility is the cornerstone of patient safety in the medical industry. You must use cleanrooms designed to meet specific standards such as ISO 5, ISO 6, and ISO 7 to guarantee an environment with a low level of pollutants. This includes utilizing High-Efficiency Particulate Air (HEPA) filters to capture particles as small as 0.3 microns.
Training for Cleanroom Operators
Cleanroom operators are required to undergo comprehensive training programs. These trainings ensure that staff are well-versed in cleanroom protocols, safety measures, and industry-specific requirements to uphold a contamination-free environment. The training covers aspects such as proper gowning procedures, correct cleaning protocols, and waste disposal methods. Mastery of these protocols is critical for maintaining a controlled environment.
Avoiding Cross-Contamination
To prevent cross-contamination, operators must follow stringent cleanroom practices, such as maintaining segregated areas for different production stages and using specialized equipment. You must adhere to practices that minimize human contact with sterile surfaces and products. Key practices include using proper airflow systems, having dedicated entry and exit pathways for personnel and materials, and ensuring the cleanroom layout is designed to prevent the spread of contaminants.
Future Trends and Innovations in Portable Cleanrooms
The cleanroom industry is rapidly evolving, with new technologies paving the way for more efficient and sustainable operations, particularly in medical device manufacturing. These advancements are set to revolutionize the way medical cleanroom solutions operate, directly benefiting the production of surgical instruments, implants, and medical device packaging.
Advancements in Cleanroom Technology
Portable cleanrooms are a significant development; you can expect customizability and scalability to become standard features. Innovations such as advanced filtration methods and smart monitoring systems are being integrated to ensure higher standards of cleanliness and control. These systems also facilitate real-time monitoring and adjustments, enhancing the overall quality control in the manufacturing of sensitive medical devices.
- Real-time Monitoring: Improved sensors for contamination detection.
- Enhanced Filtration: HEPA and ULPA filters for nanoscale particles.
Cleanrooms and Environmental Sustainability
Your cleanroom's environmental impact is now a priority. Manufacturers are developing energy-efficient cleanroom solutions that not only meet regulatory standards but also reduce carbon footprints. Technologies that support energy recovery, such as HVAC systems with variable speed fans, are becoming commonplace, ensuring that you maintain a sterilized environment while conserving energy.
- HVAC Efficiency: Variable speed fans for optimal energy use.
- Sustainable Materials: Construction with recycled and eco-friendly materials.
Growth of Portable Cleanrooms in the Medical Sector
The medical sector's demand for portable cleanrooms is on the rise, driven by the growing need for sterile medical device packaging and the rise in the production of surgical instruments and implants. New medical cleanroom solutions are emerging to support this growth, catering to the stringent regulations of the sector and the need for precision in manufacturing.
- Modular Design: Tailored cleanrooms that fit medical manufacturing needs.
- Regulatory Compliance: Solutions aligning with FDA and international standards.
The integration of innovation within cleanrooms enables you to maintain strict hygienic conditions, crucial for the safety of medical devices. These are not mere upgrades; they are essential steps forward in the world of medical manufacturing, ensuring patient safety and product efficacy.
Coffee junkie. Spoonie. Writer about all things chronic illness and mental health. Friend of animals everywhere.
Dr. Wilson graduated from Rosalind Franklin University of Medicine and Science and completed her residency in Internal Medicine at Advocate Good Shepherd Hospital in Barrington, IL. Dr. Wilson specializes in providing culturally competent and trauma-informed care to patients with physical disabilities. In addition to her private practice, she works as a science communicator, teaching health literacy to middle school and high school students in her local school district.